Single family homes: Baking 1000 cookies with 1000 cookie-cutters
Marc Andreessen publicly claimed that “fully loaded construction costs [for end consumers] have doubled” since the year 2000. While the research wizards in our Foundamental Insights group couldn’t corroborate the exact number Marc was referring to, we did triangulate with primary research done by the NAHB and US Census Bureau.
Marc Andreessen publicly claimed that “fully loaded construction costs [for end consumers] have doubled” since the year 2000. While the research wizards in our Foundamental Insights group couldn’t corroborate the exact number Marc was referring to, we did triangulate with primary research done by the NAHB and US Census Bureau.
‘Each situation requires a new architecture’
— Jean Nouvel
Our findings: single family homes (SFHs) in the US were 88% more expensive in 2017 than in 1998. Quite close to Marc’s number. So what’s up here? Is it that houses got bigger? (they do, but only by 100–200 square feet). Is it that construction companies take a higher profit today? (mostly they don’t). Are costs for the underlying materials and components exploding? (they are not). Or is our cookie-cutter: cookie ratio maybe close to 1:1?
Here are my 10 slices on SFH building costs:
1/ The share of spec homes — homes that have a standard floor plan and specifications — rose to 80% in the US in 2017, up from 71% in 2010. Vice versa, custom homes had a share of only 20% in 2017.
2/ So: the proliferation of spec homes suggests an increasing standardization in the US home building industry.
3/ One way to see the impact of standardization would be in the bottom lines. But: Developer’s operating profit margins hover around 10% to 16% profit per single family home built. In real money terms: $45k to $65k. Surprised their bottom line is not higher? SFH construction companies who also act as developer and broker themselves are able to increase their bottom line per home by an additional 5–8%, bringing the total operating profit to 15–24% in most cases.
4/ Another way to check for efficiency is the speed of completion. But: Average cycle times from start to completion of new SFH increased from 9 months in the mid 1990s to 11.5 months in 2018. Again, the increasing standardization of SFH did not lead to shorter production and development times.
5/ One root cause: The construction labor crisis. Imagine Henry Ford had the T-Model blueprint and line, but had to bring in a new factory worker for every produced unit.
6/ But an even bigger root cause: the complexity of SFH has increased significantly. The share of homes which have production cost >$100 per sq. ft. was at 62% in 2018, up from 20% in 2002.
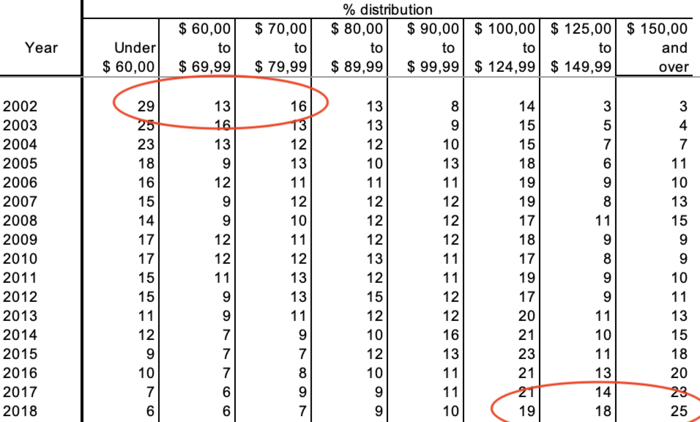
7/ A third key cause is: SFHs are usually built with framing and foundation, which has not been automated to date. 10% of SFH cost are for the foundation and another 17% for the framing, trusses, and sheathing. These tasks today remain highly labor intensive.
8/ And: a fourth cause is the low automation of exterior finishing. 14% of the SFH cost are used up by roofs, windows, doors and exterior walls finishing. All of these tasks remain highly labor intensive to date.
9/ But: Often times we hear that MEP (mechanical, electrical and plumbing) are a major cost driver of construction costs. While MEP installation is labor intensive, the numbers don’t support that MEP is a major efficiency lever. While 13% of SFH cost are associated with MEP incl. HVAC, less than half of those cost allocate to the installation labor. The production of the MEP material and systems already happens in factories. That brings the controllable/optimizable cost of MEP down to only an estimated 5–6% of the total SFH cost. Given the complexity of automating the installation of MEP this shouldn’t be a high priority for automation.
10/ Ergo: The numbers prove that even in cookie-cutter homes (a) the complexity of homes has continously increased and (b) even though homes are built in cookie-cutter layouts, the raw structures from foundation to exterior wall paint remain highly labor-intensive for every build and make up one third of the overall cost. To use a baking analogy: SFH home builders have cookie-cutters, but they are forced to carefully place the cookie dough in each cookie cutter, one by one.
Founder opportunities could be:
Find ways to automate the production + assembly of the shell structure. Either by redefining how the shell structure is engineered and produced — like the incredibly smart team over at our portfolio company Mighty Buildings have done by printing with a unique polymer — or by automating the labor of each current work step, like a company we have recently met which fully automates the assembly of timer framing. This approach addresses one third of an SFH’s total cost.
Mass-produce and mass-install foundations. Foundations make up 10% of an SFH’s cost — on average $30–40k. Today, they are treated custom to every home. The labor-intensive part is the excavation and framing. Any tech firm that can get keep the dirt in place and doesn’t need to install foundation framing on site might be able to reduce SFH cost by as much as 5% or more, by our estimates.
Attack in lower-spec niches. The rise in the tiny homes segment is encouraging, but we have yet to see a company that has achieved high production automation and consistency in low-spec homes and disrupt their way up from there. The closest are still “manufactured homes”. (ie. RVs), which have been around for decades. It also explains private equity’s recent surge in interest in consolidating the manufactured home market. The big opportunity for founders is to produce a high UX, highly digital, home below $100k and above 500 square feet in less than 60 days.
Sources:
- SFH = Single family homes
- National Association of Home Builders
- Harvard University, Joint Center for Housing Studies
- US Census Bureau