Multiple sources claim that ready-mixed concrete (RMC) is the second most used substance after water. While we did not validate this exact assessment we know that RMC is vastly used throughout the world. Yearly production rates are at ~270 mn cubic meters in the US and ~330 mn cubic meters in Europe. In India, however, concrete is predominantly mixed on site leading to a lower production volume of RMC which is at 90 mn cubic meters.
RMC is a quasi-commodity and its production not a state secret. But: the devil is in the delivery.
‘That in which our calculations fail, we call coincidence.’
— Albert Einstein
The delivery of RMC requires specific trucks that can only be used for exactly that purpose.
Once water has been added to the mix, the RMC has to be discharged on the job site within 60–90 minutes at max.
The optimal temperature to pour RMC ranges from 5°C to 30°C. Outside of this interval pouring gets difficult. Direct exposure to wind and sun makes it even more tricky.
In order for the truck driver to be able to discharge the RMC the job site needs to be ready. That not only implies that preliminary workflows such as installation of framework or rebar need to be finished, but also that access routes are clear and — if required — concrete pumps, cranes, and concrete buckets are available.
At Foundamental, we like to invest in companies that are orchestrating supply chains in the construction industry of tomorrow — in RMC dispatching there is still work to be done.
Here are my 10 slices on RMC Dispatching:
1/ The fulfillment of ready-mixed concrete (RMC) deliveries is regarded as a core competency by materials suppliers. On average, RMC producers own 90% of the RMC trucks they use.
2/ And: Profitability of RMC producers ranges between 4%-8% of their net sales. To maintain this level of profitability, companies need to maximize their RMC trucks’ utilization.
3/ But: RMC demand is not equally distributed but highly clustered around certain peak hours.
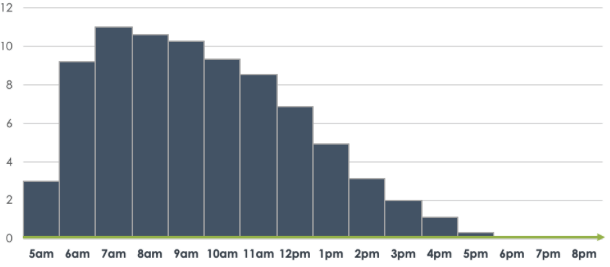
4/ Ergo: To increase asset utilization RMC producers max out their trucking capacities and overbook their delivery slots by varying degrees — if you want to know how that affects RMC truck drivers check out this blog article. Anticipating this behavior and accounting for unpredictable factors like weather and construction site progress, nifty contractors place “ghost orders” to make sure their delivery gets fulfilled at the quantity and timing they want.
5/ Ergo: Roughly 40% of the RMC orders do not get delivered as scheduled — 28% are moved to another date while 12% are cancelled. And: how are these changes being communicated? 100% in person via phone in which usually more annoyances than information are exchanged.
6/ In the past years the most common approach to improve this process’ efficiency was either to replace phone calls by new mobile applications or to use multi parameter optimizer software to optimally allocate trucks and orders.
7/ But: to our knowledge those optimizers or applications have not achieved a level of customer experience and efficiency as Amazon has for example.
8/ Why? The dependencies of RMC deliveries on weather, construction site progress, availability of workforce etc. cannot be removed in the near future. And: the way information among contractors and RMC suppliers are exchanged today (= mostly by phone) is not suitable to (1) capture and (2) share relevant data live and in a computer-processable way.
9/ Ergo: Every efficiency optimization operates under limited information quality and quantity by definition and can hence only lead to a local optimum.
10/ But: at Foundamental, we see that startups in construction tech are starting to build large datasets by closely monitoring the status and progress on construction sites. Examples are the folks at Veyor and Indus.AI. Sharing and connecting those different datasets will ultimately enable an orchestrated RMC dispatching.
Sources:
- Foundamental field research, 2018 and 2019
- Foundamental deal flow and due diligence, 2018 and 2019
- Statista